Types of Iron Castings
This chapter will discuss the various types of iron castings.
Gray Iron Casting
The characteristic of gray cast iron is the graphic microstructure, which is able to cause fractures to the material and have a gray appearance. This one is the most commonly used type of cast iron and also commonly used cast material based on weight. A majority of the gray cast irons have a chemical decomposition of 2.5 percent to 4 percent carbon, 1 percent to 3 percent silicone and the rest is a composition of iron.
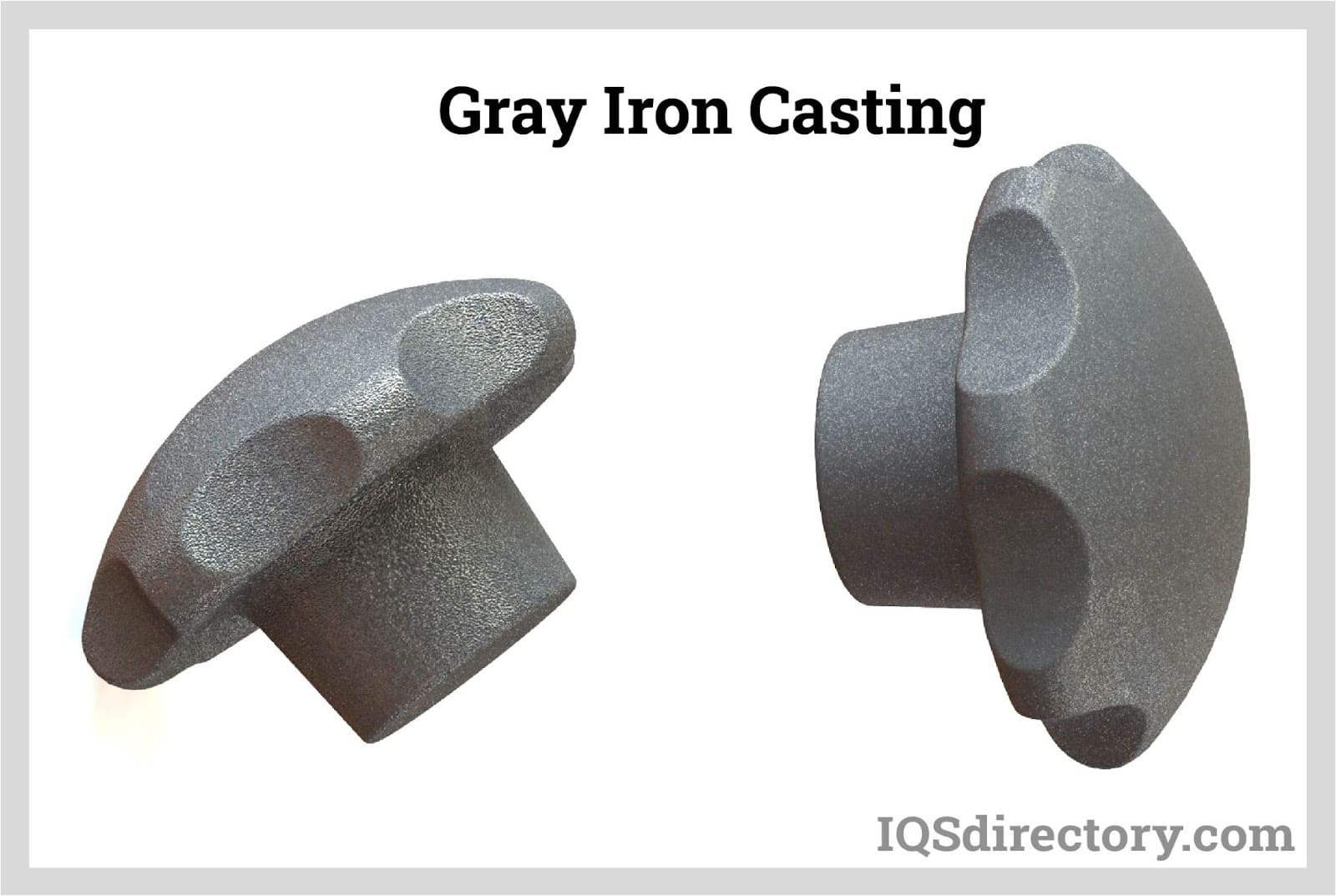
This type of cast iron has less tensile strength and less resistance to shock compared to steel. Its compressive strength is comparable to low and medium carbon steel.
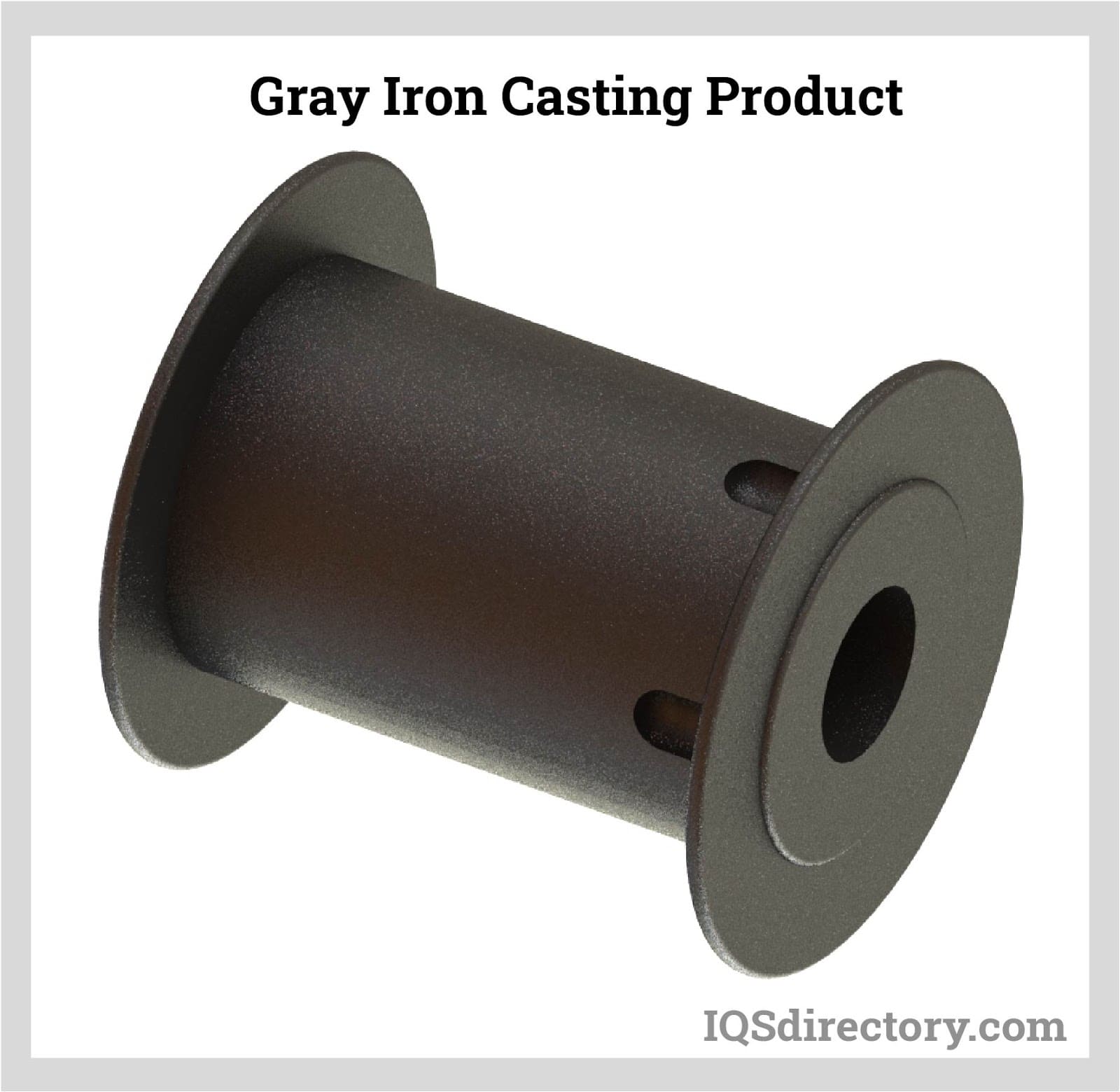
All these mechanical properties are controlled by the graphite flake‘s shape and the size of the graphite flakes, which are present in the microstructure of the gray cast iron.
White Iron Casting
This type of iron has fractured surfaces which are white due to the presence of an iron carbide precipitate named cementite. The carbon that is contained in white cast iron precipitates out of the melt as met stable phase cementite rather than as graphite. This is achieved with lower silicon content as the graphitizing agent and a faster supplied cooling rate. After this precipitation, the cementite forms as large particles.
During the precipitation of the iron carbide, the precipitate draws carbon from the original melt, thus moving the mixture toward one that is closer to eutectic. The remaining phase is lowering iron to carbon austenite, which transforms to martensite once cooled.
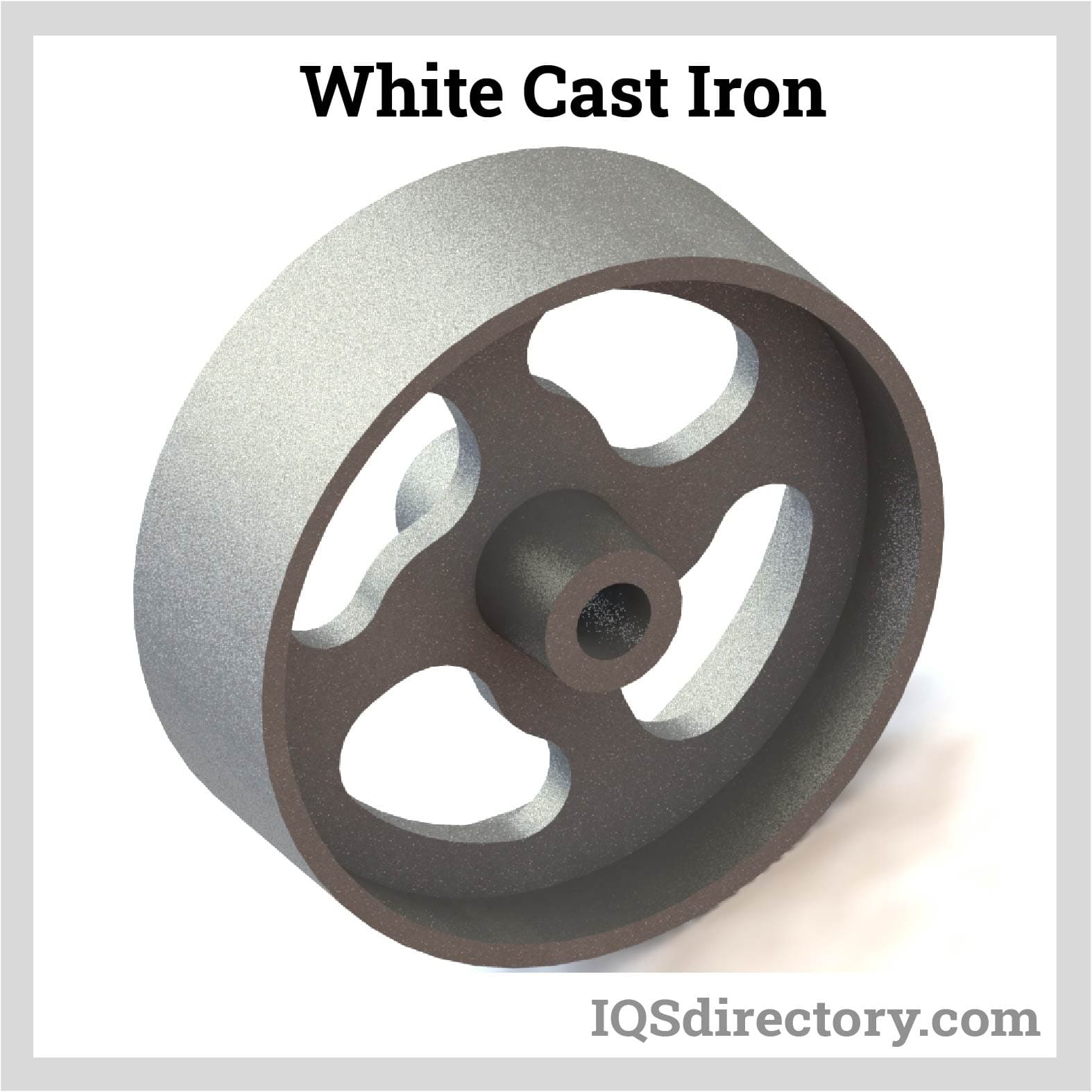
These contained eutectic carbides are too large to provide the benefit of precipitation hardening. In some steels there might be much smaller cementite precipitates that might carry the deformation of plastic by impeding the movement of dislocations through the pure iron ferrite matrix. They have an advantage as they increase the bulk hardness of the cast iron simply because of their own hardness and volume fraction. This results in the bulk hardness being able to be approximated by a rule of mixtures.
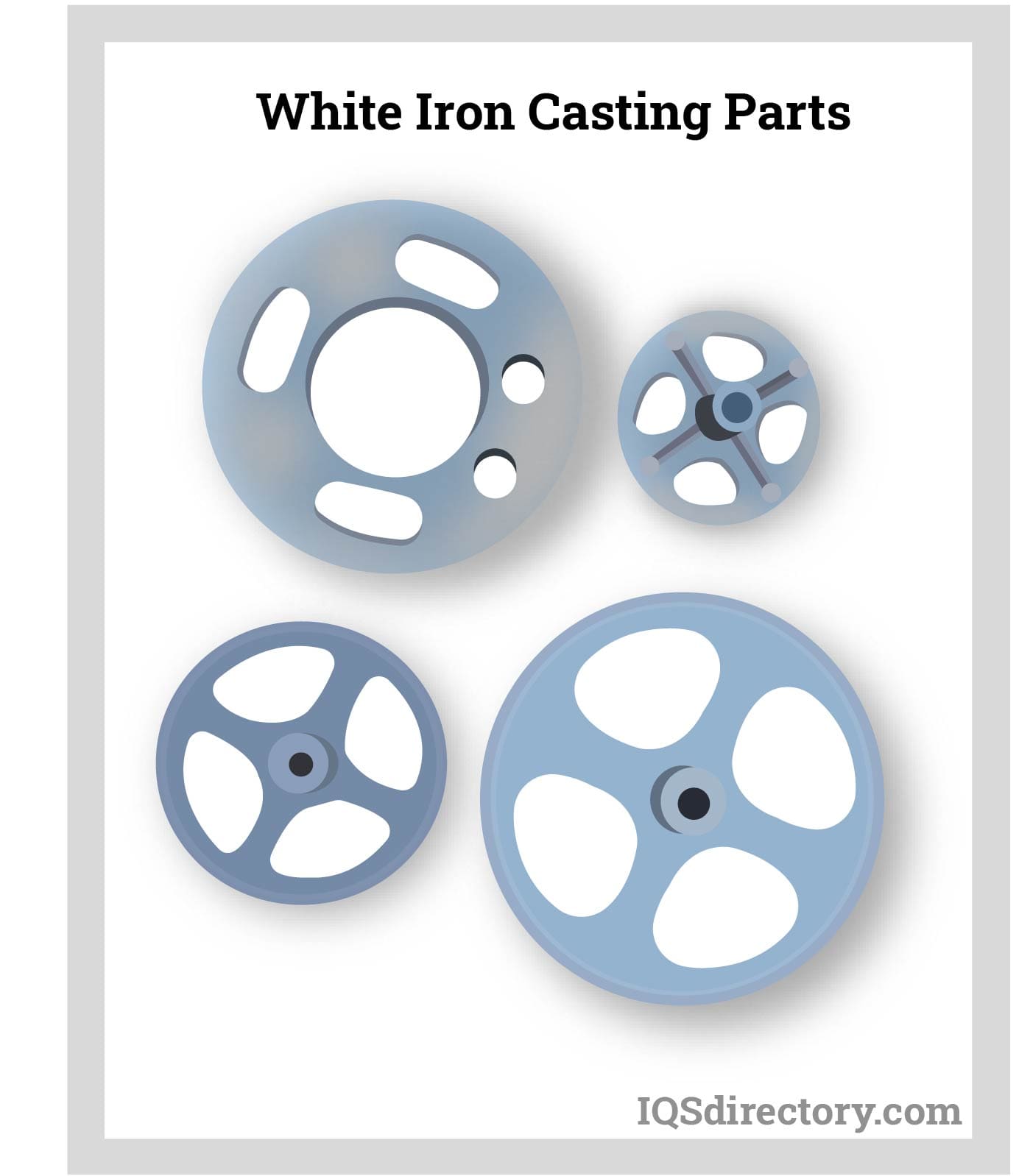
This hardness is offered at the expense of toughness in any case. White cast iron can be generally classified as a cement, since carbide makes up a larger fraction of the material. White iron is too brittle to be used in structural components, but because of its good hardness, resistance to abrasion, and low cost, it can be used as the wear surface of slurry pumps.
It is hard to cool thick castings at a faster rate which is enough to solidify the melt as white cast iron, however rapid cooling can be put to use in order to solidify a hell of white cast iron and after this a remainder of it will be cool at a slower pace thus forming a core of gray cast iron. This resulting cast is called a chilled casting, and it contains the benefits of having a hard surface but with a tougher interior.
High chromium white iron alloys had an ability of allowing massive casting of about a 10 tonne impeller to be sand cast. This is due to the fact that the chromium reduces the cooling rate required to produce carbides through the greater thicknesses of material. Carbides with an excellent abrasion resistance are also produced by chromium elements.
Malleable Iron Casting
Malleable cast iron begins as a white iron casting, then heat treated at temperatures of about 950°C for two or a single day, and then it is cooled for the same period of time.
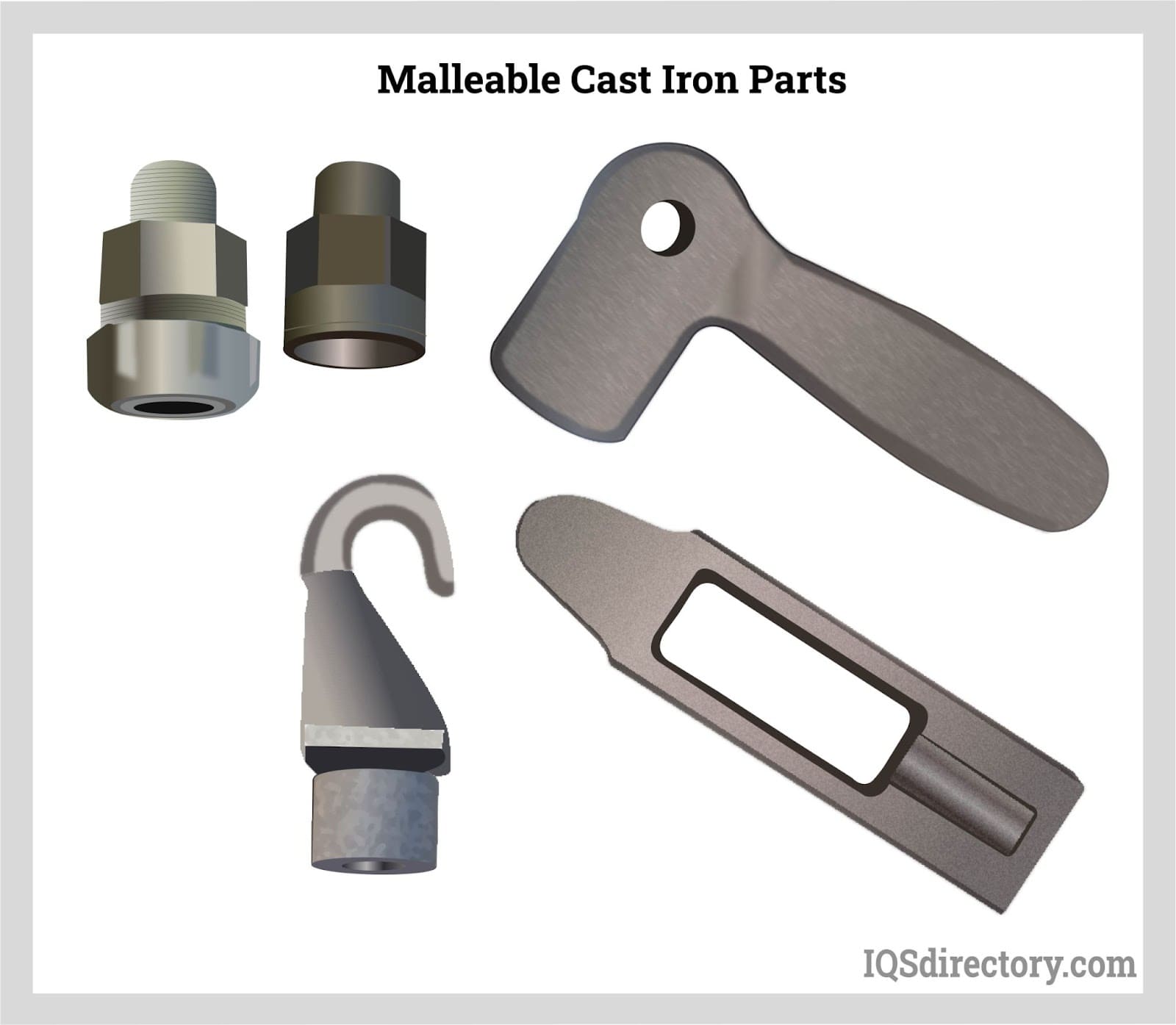
The carbon in iron carbide then transforms into graphite and ferrite plus carbon due to this heating and cooling process. This is a low process, but it enables the surface tension to transform the graphite into spheroidal particles rather than flakes.
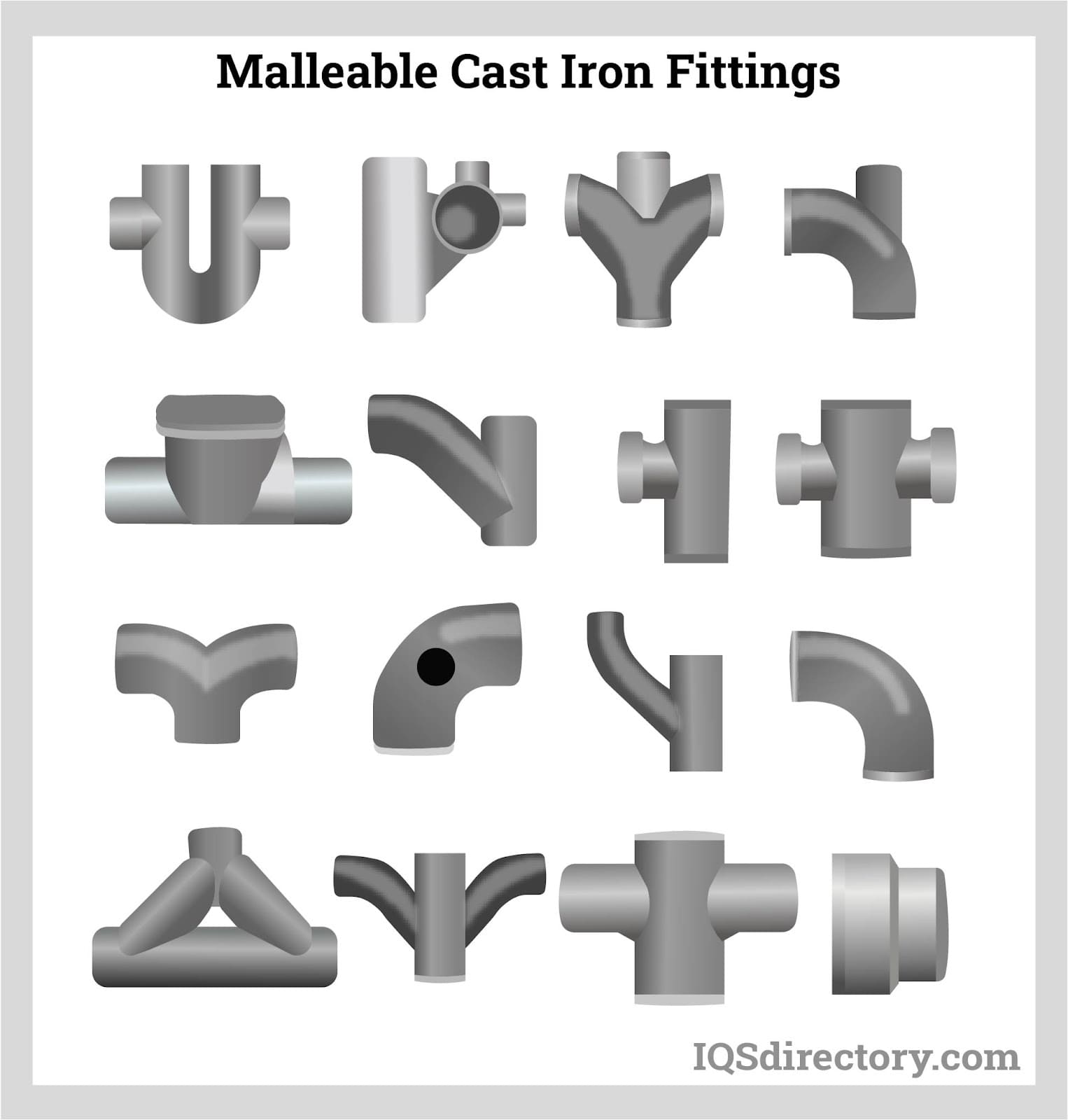
The spheroids are relatively short and further away from each other due to their low aspect ratio. They also contain a lower cross-section, propagating crack and a photon. As opposed to flakes, they contain blunt boundaries which partake in the alleviating of the stress concentration problems which are found in gray cast iron. All in all, the properties included in the malleable cast iron are more like those of steel which is mild in nature.
Ductile Iron Casting
Sometimes referred to as nodular cast iron, this cast iron has its graphite in the form of very tiny nodules, with the graphite having the form of layers which are concentric and thus forming the nodules. Due to this, the properties of ductile cast iron are that of a spongy steel which has no stress concentration effects produced by the flakes of the graphite.
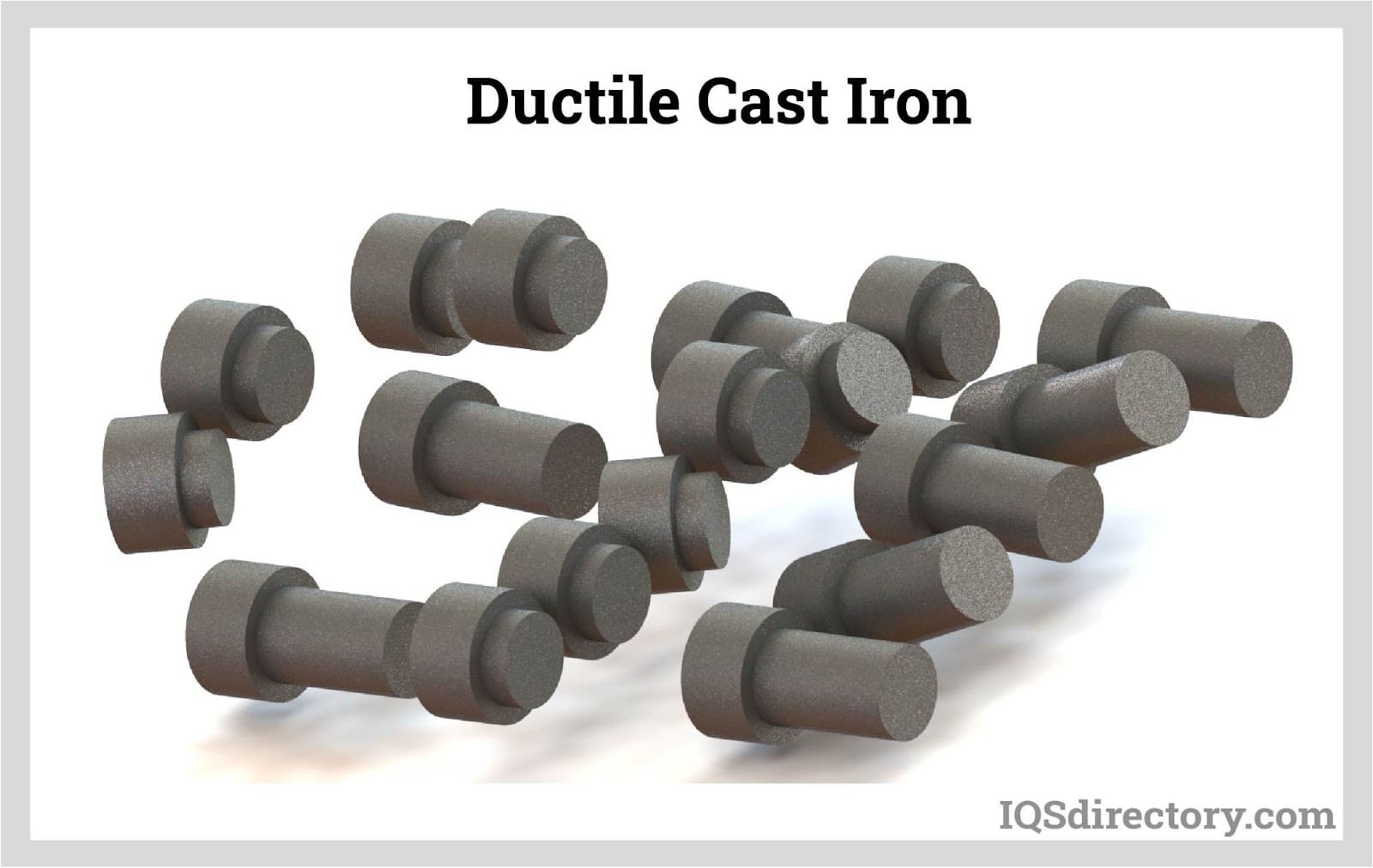
The carbon concentration amount contained is around 3 percent to 4 percent, and that of silicon is around 1.8 percent to 2.8 percent. Small amounts of 0.02 percent to 0.1 percent of magnesium, and only 0.02 percent to 0.04 percent cerium when added to these alloys slows down the rate at which graphite precipitation grows through bonding to the graphite lanes edges.
Carbon can have a chance of separating as spheroidal particles as the material solidifies, due to the careful control of other elements and proper timing during the process. The resulting particles are similar to malleable cast iron, but parts can be cast with sections that are larger.
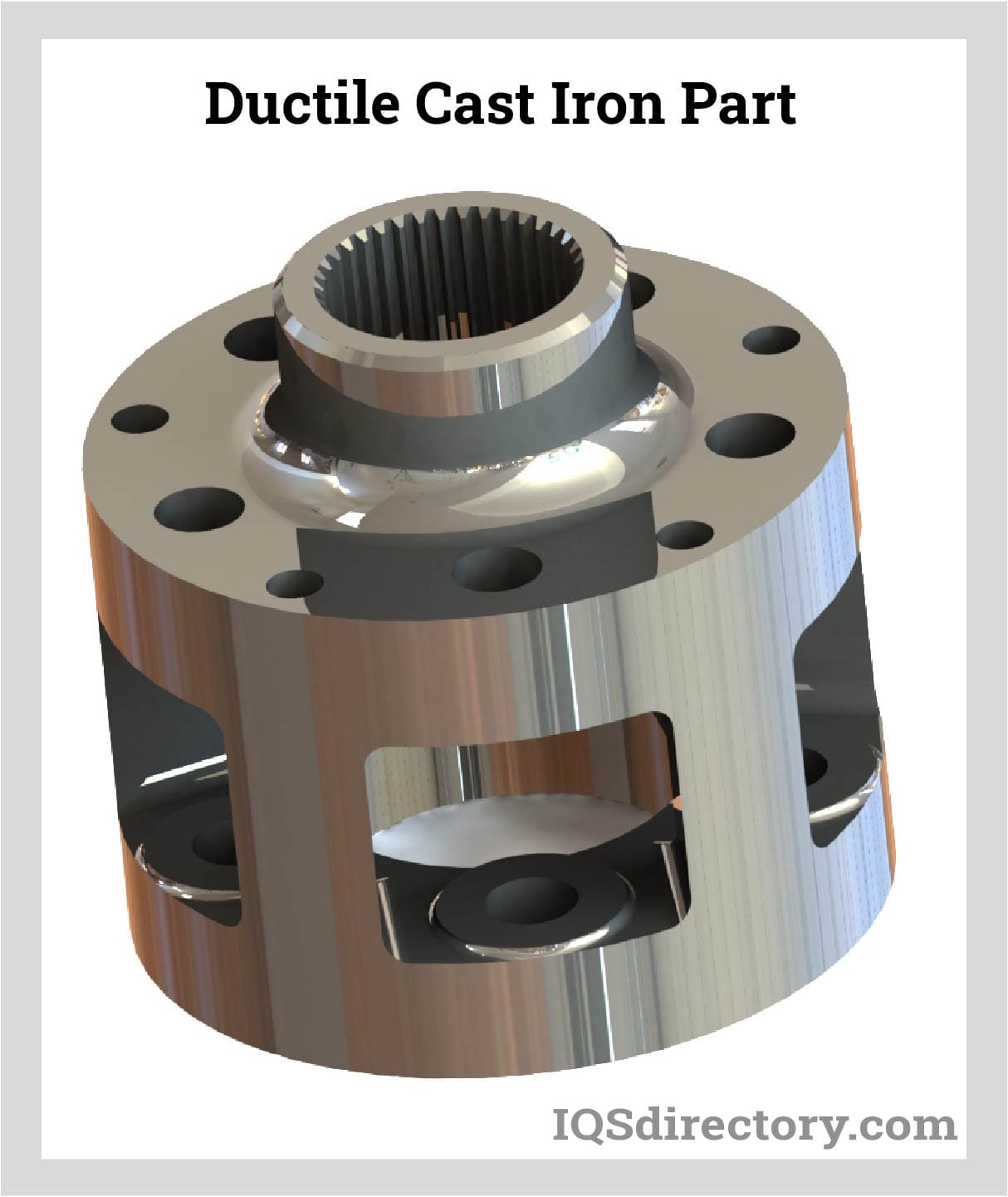
Alloying Elements
The properties of cast iron are changed and added in various alloying elements or alloyants in the cast iron. In line with carbon is the element silicon because it has an ability to force carbon out of the solution. A smaller percentage of silicon can not be able to fully achieve this as it allows carbon to remain in the solution, thus forming iron carbide and also producing white cast iron.
A bigger percentage or concentration of silicon is able to force the carbon out of the solution and then form graphite and also produce gray cast iron. Other alloying agents not noted include manganese, chromium, titanium and then vanadium. These counteract silicon, they also promote the retention of carbon and thus also the formation of carbides. Nickel and the element copper have an advantage as they increase strength and machinability, but they do not then be able to change the amount of carbon formed.
The carbon that is in the form of graphite results in a softer iron, thus reducing the effect of shrinkage, lowering the strength and decreasing the contained density. Sulfur is mostly a contaminant when contained, and it forms iron sulfide which prevents the formation of graphite and also which increases hardness.
The disadvantage imposed by sulfur is that it makes molten cast iron viscous, which causes defects. To cater for and eliminate the effects of sulfur, manganese is added to the solution. This is done because when the two are combined they form manganese sulfide instead of iron sulfide. Resulting manganese sulfide is lighter than the melt and tends to float out of the melt and get into the slag.
The approximate amount of manganese needed to cancel out the effects of sulfur is 1.7 units of sulfur content and an additional 0.3 percent added on top. The adding of more than this amount of manganese results in the formation of manganese carbide and this increases hardness and chilling except in gray iron where up to 1 percent of manganese can increase strength and the density contained. Nickel is one of the most general alloying elements because it has a tendency of refining the pearlite and the structure of the graphite, thus improving the toughness, and evens out the hardness difference between section thicknesses.
Chromium is added in small amounts to reduce free graphite and produce a chill. This is because chromium is a powerful carbide stabilizer, and in some cases it can work in conjunction with nickel. For chromium also, a small substitute amount of tin can be added. Copper is added in the ladle or furnace on the order of 0.5 percent to 2.5 percent to achieve a lowering chill, refining graphite, and the increment in fluidity. Molybdenum can also be added in the order of 0.3 percent to 1 percent so as to also increase the chill, refine the graphite, and refine the pearlite structure.
It is usually added working in line with nickel, copper, and chromium to produce high strength irons. The element titanium is added to work as a degasser and a deoxidizer, and increase fluidity. Proportions of 0.15 percent to 0.5 percent of the element vanadium are added to the cast iron and help in stabilizing cementite, to increase hardness and resist wear and heat effects.
Zirconium helps form graphite and is added in proportions of about 0.1 percent to 0.3 percent. This element also helps in deoxidizing and increasing fluidity. In malleable iron melts, to increase how much silicon can be added, bismuth is poured in a scale of 0.002 percent to 0.01 percent. In white iron, the element boron is added,which aids in the production of iron which is malleable, and it reduces the coarsening effect of the element bismuth.